Understanding Electric Injection Machines in the Metal Fabrication Sector
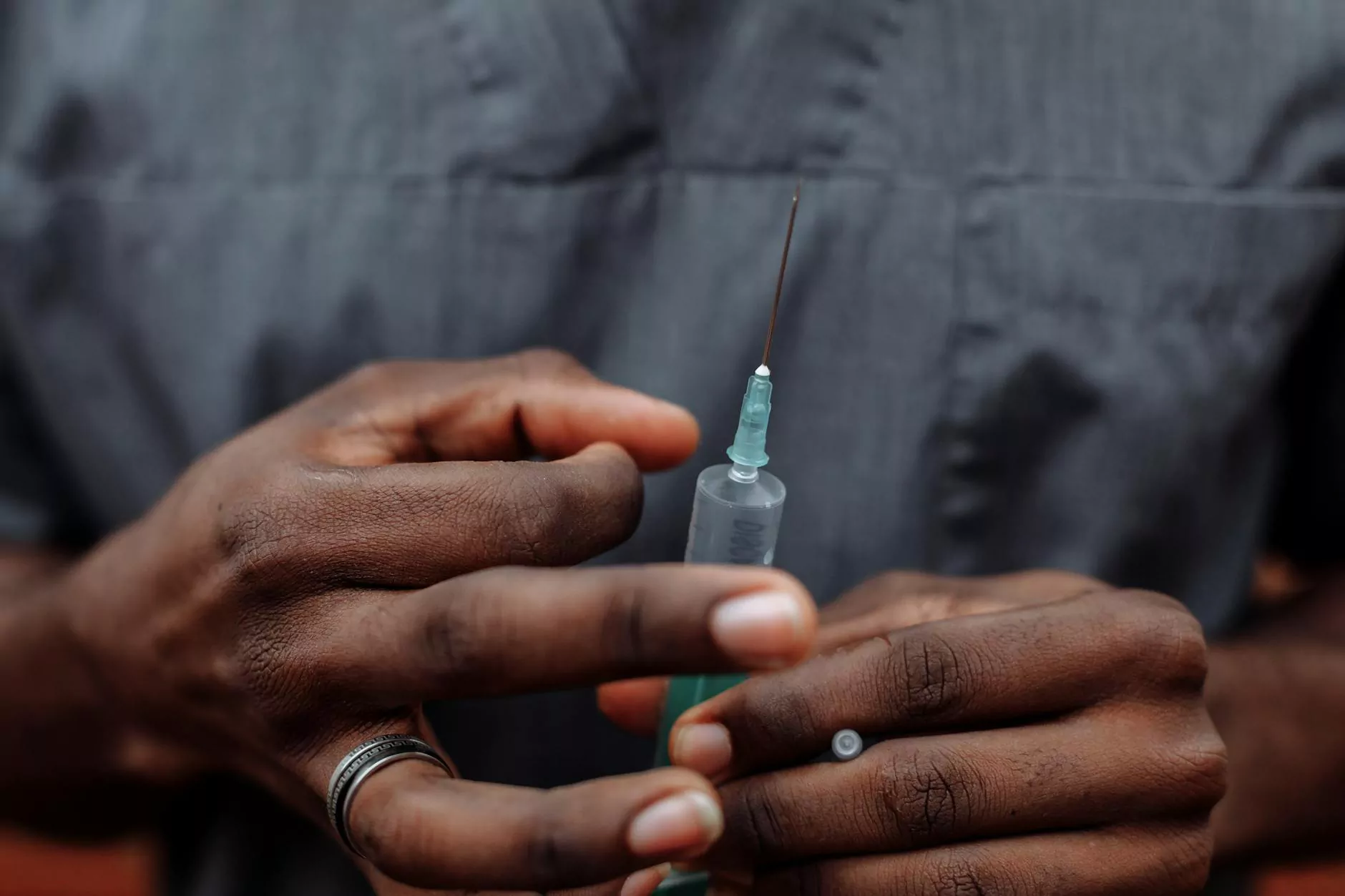
The electric injection machine is revolutionizing the way manufacturers approach the production of various components. As industry needs evolve, the demand for more efficient, precise, and environmentally friendly manufacturing processes has never been greater. In the realm of metal fabricators, the transition to electric machines is not just another trend, but a significant shift toward sustainability and superior production quality.
What is an Electric Injection Machine?
The electric injection machine operates by using a fully electric system to inject molten materials into molds. Unlike traditional hydraulic systems, these machines utilize servo motors and electric actuators to provide superior precision and speed. This technology minimizes energy consumption while maximizing output quality, making it an excellent choice for various manufacturing sectors.
Key Components of an Electric Injection Machine
- Injection Unit: This is responsible for heating and injecting the material.
- Screw Drive: It is used to mix and convey the raw material.
- Mold Clamping Unit: This section holds the mold securely during the injection process.
- Control System: Modern electric injection machines come with sophisticated software for better precision and control.
Benefits of Electric Injection Machines
Switching to electric injection machines offers numerous advantages over traditional hydraulic options. Below are some of the most notable benefits that make them the preferred choice for many manufacturers:
1. Energy Efficiency
One of the most compelling reasons to invest in an electric injection machine is its energy efficiency. Electric machines consume significantly less power compared to hydraulic machines, leading to lower operational costs. Industries are increasingly focused on sustainability, and the reduced energy footprint of electric machines aligns with these environmental goals.
2. Enhanced Precision
Electric injection machines provide consistent and repeatable results, offering precise control over injection speed, pressure, and temperature. This level of accuracy is crucial for industries that demand tight tolerances and high-quality outputs, such as automotive and aerospace manufacturing.
3. Reduced Maintenance Costs
With fewer moving parts and no hydraulic fluids involved, electric injection machines require less maintenance than their hydraulic counterparts. This factor can lead to significant savings for manufacturers in the long run, as downtime for repairs and maintenance is minimized.
4. Improved Working Environment
Electric machines are generally quieter and generate less heat than hydraulic machines, thus improving the workplace environment. This reduction in noise pollution can enhance worker satisfaction and productivity, creating a better overall atmosphere in manufacturing facilities.
Applications of Electric Injection Machines in Metal Fabrication
The versatility of the electric injection machine makes it suitable for a broad range of applications within metal fabrication. Here are some key areas where these machines are proving invaluable:
1. Automotive Parts Manufacturing
Electric injection machines are increasingly used to manufacture complex automotive parts with high precision. This technology enables the production of lightweight and durable components, which are essential in the drive for fuel-efficient vehicles.
2. Aerospace Components
The aerospace industry demands exceptionally high standards, and the precision offered by electric injection machines meets those requirements. These machines facilitate the production of intricate parts used in aircraft, ensuring safety and reliability.
3. Consumer Electronics
In the production of consumer electronics, tight specifications and quick turnarounds are crucial. Electric injection machines provide the flexibility and speed needed to meet these demands, enabling manufacturers to stay competitive in a rapidly changing market.
Choosing the Right Electric Injection Machine
Considering the investment involved, selecting the right electric injection machine requires careful thought. Here are some factors to contemplate:
1. Production Needs
Understand your production requirements in terms of capacity, types of materials used, and the complexity of the parts to be manufactured. An electric injection machine should align with your operational goals.
2. Size and Configuration
The physical size and configuration of the machine matter greatly. Ensure that the machine can fit within your current workshop layout and has the necessary clamping force for your projects.
3. Budget
While electric injection machines can have a higher upfront cost, their long-term savings on energy and maintenance should also be taken into account. Assess your budget, keeping in mind the overall lifecycle costs.
4. Supplier Reputation
Research suppliers to find reputable manufacturers of electric injection machines. Evaluate their customer service, warranty options, and support for training and maintenance.
Future Trends in Electric Injection Machines
As technology advances, the electric injection machine industry continues to innovate. Here are some future trends to watch:
1. Smart Manufacturing
With the rise of Industry 4.0, smart manufacturing technologies are likely to integrate with electric injection machines, enabling real-time monitoring and adjustments to optimize production processes.
2. Eco-Friendly Materials
The demand for more sustainable materials will push electric injection machines to adapt and innovate further, focusing on recyclable and biodegradable options.
3. Automation and Robotics
Future electric injection machines may incorporate robotics for handling and assembly, further enhancing productivity and reducing labor costs.
Conclusion
Investing in an electric injection machine is a strategic move for metal fabricators aiming to enhance their efficiency, precision, and sustainability. As industries continue to evolve, those businesses that embrace electric technology will be better positioned to meet future challenges and demands. By understanding the benefits, applications, and future trends, manufacturers can make informed decisions that propel them ahead of their competition.
For further insights and high-quality machinery, visit DeepMould.net, your top resource for advanced manufacturing technology and support.