The Comprehensive Guide to Plastic Mould Manufacture
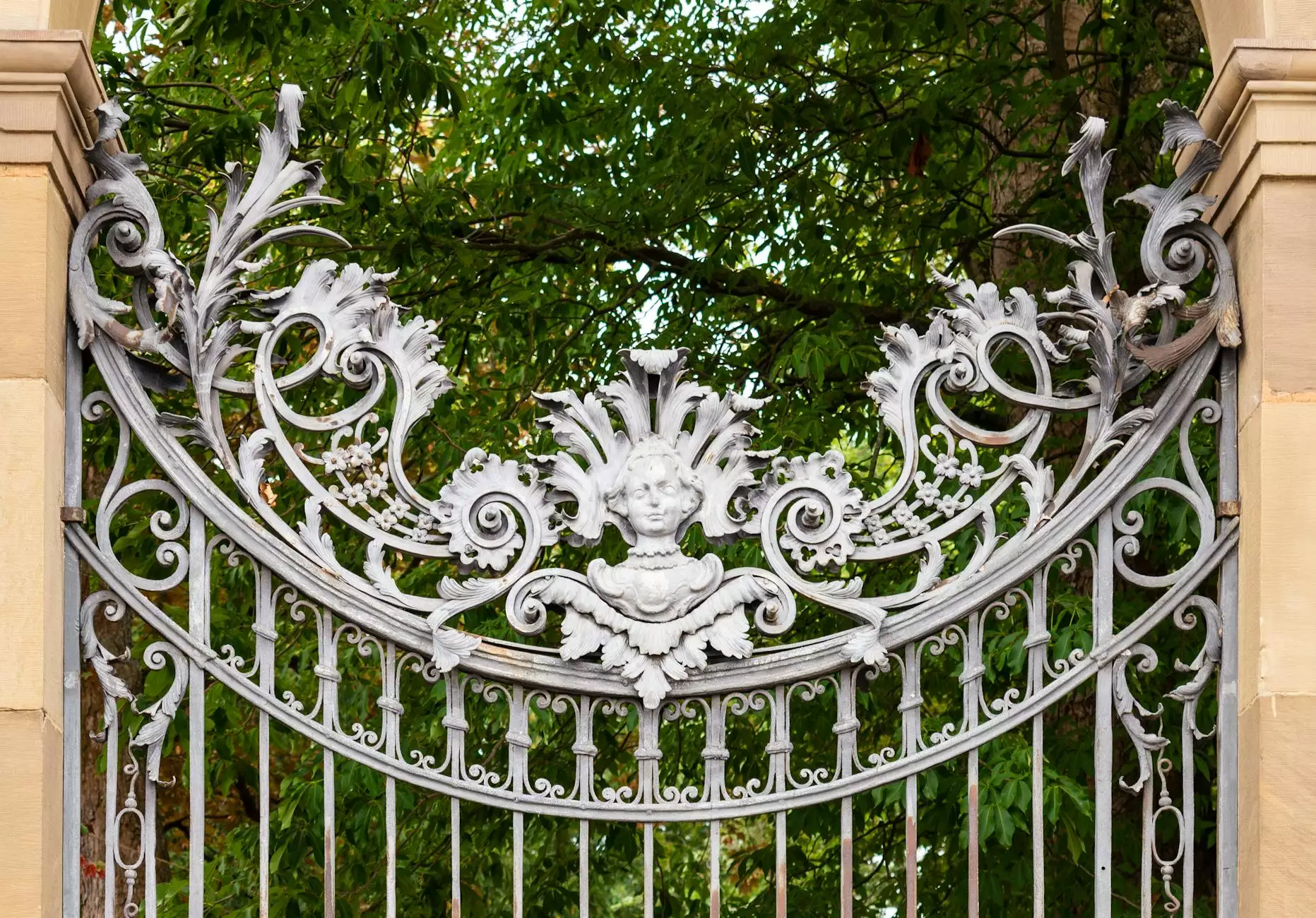
In today's fast-paced manufacturing landscape, plastic mould manufacture has emerged as a pivotal aspect of many industries. Whether you are producing consumer goods or intricate industrial components, understanding this process is imperative. This article delves deeply into the nuances of plastic mould manufacture, focusing on its techniques, benefits, and industry trends, particularly through the lens of our experience at Hanking Mould.
Understanding Plastic Moulding
Plastic moulding is a manufacturing process that involves creating objects by heating and shaping plastic materials in a form or mould. The fundamental steps in this process generally include:
- Material Selection: Choosing the right plastic based on strength, flexibility, and durability requirements.
- Mould Design: Engineering the mould to achieve the desired shape and functionality of the final product.
- Injection Process: Melting the plastic and injecting it into the mould, where it cools and solidifies into the final shape.
- Finishing: Removing the part from the mould and applying any necessary surface treatments.
The Importance of Plastic Mould Manufacture in Industry
The application of plastic mould manufacture extends across various sectors:
- Automotive: Production of dashboards, panels, and various car components.
- Consumer Electronics: Enclosures for mobile phones, computers, and household appliances.
- Healthcare: Manufacturing of medical devices, packaging, and disposable items.
- Packaging: Creating custom packaging solutions that are both functional and aesthetically pleasing.
Benefits of Plastic Moulds
Investing in plastic mould manufacture offers several benefits that can enhance production efficiency and product quality:
1. Cost-Effectiveness
One of the primary advantages of plastic mould manufacture is its cost-effectiveness, particularly for large production runs. The initial investment in mould design and fabrication may be high, but the per-unit cost drops significantly as production volumes increase. This process allows businesses to achieve higher margins and reduce overall production costs.
2. Precision and Consistency
Modern moulding techniques allow for remarkable precision and repeatability, ensuring that every part produced is uniform. This consistency is crucial in industries where quality and specifications are paramount, such as automotive and medical applications.
3. Design Flexibility
Plastic mould manufacture supports a wide array of designs, from simple geometric shapes to intricate patterns. Advanced simulation software aids in optimally designing moulds to suit various specifications. Businesses can also implement design changes without significant retooling costs, making adaptation to market demands more manageable.
4. Rapid Prototyping
Creating prototypes quickly is essential for testing concepts and designs. Using plastic injection moulds, manufacturers can produce prototypes in days rather than weeks, allowing for faster iterations and quicker time to market for new products.
Innovations in Plastic Mould Manufacture
The world of plastic moulding is evolving continually with technological advancements. Here are some key trends currently shaping the industry:
1. Automation and Robotics
The integration of automation technologies is transforming the plastic moulding industry. Automation streamlines the production process, reduces human error, and enhances efficiency. Robotic systems can handle intricate tasks such as loading materials, handling finished products, and maintaining quality inspections, leading to higher throughput and lower labor costs.
2. Sustainable Practices
With rising environmental concerns, the push for sustainability is more prominent than ever. Manufacturers are increasingly focusing on using recyclable plastics and incorporating eco-friendly practices into their processes. Hanking Mould is committed to sustainable production methods, striving to minimize waste and reduce our carbon footprint.
3. Advanced Material Use
The development of new plastic formulations, including bio-based and composite materials, expands the potential applications of moulding. These materials often offer enhanced performance characteristics such as improved strength, heat resistance, and overall durability.
Types of Moulds in Plastic Mould Manufacture
Different types of moulds serve various purposes in plastic mould manufacture. Understanding these types can help businesses select the right mould for their specific needs:
- Single cavity moulds: Designed to create one part per cycle, ideal for low-volume production.
- Multi-cavity moulds: Can produce several identical parts in one cycle, increasing production efficiency for high-volume runs.
- Family moulds: Allow the creation of different parts in a single mould, reducing the need for multiple setups.
- Two-shot moulds: Enable the use of two different plastics in one piece, combining functionality and aesthetics.
The Role of Quality Assurance in Plastic Mould Manufacture
Quality assurance is a critical aspect of the plastic mould manufacture process. Without rigorous testing and inspection, defects can lead to costly recalls and diminished consumer trust. Companies like Hanking Mould employ stringent quality control measures, including:
1. In-Process Inspection
Regular checks throughout the production process ensure that deviations from specifications are caught early, which can significantly reduce waste and rework time.
2. Final Product Testing
Upon completion of production, thorough evaluations are performed. This includes stress testing and dimensional checks to guarantee that the finished products meet the required standards.
3. Customer Feedback Integration
Consistently gathering and analyzing customer feedback helps companies refine their processes and products, leading to continuous improvement in quality.
Partnering with a Leading Plastic Mould Manufacturer
When considering plastic mould manufacture, choosing the right partner is critical. Hanking Mould specializes in producing high-quality plastic injection moulds tailored to our customers' needs. Our strengths include:
- Expertise: Our team is comprised of experienced engineers and designers skilled in advanced moulding technologies.
- Customer-Centric Approach: We prioritize our clients' needs, offering customized solutions and dedicated support throughout the project lifecycle.
- State-of-the-Art Facilities: Equipped with the latest machinery and technology to ensure precision and efficiency in our manufacturing processes.
- Comprehensive Services: From design to production, assembly, and even post-production support, we cover every step in the plastic moulding journey.
The Future of Plastic Mould Manufacture
The future of plastic mould manufacture looks bright. As industries continue to demand innovations and efficiencies, manufacturers who embrace the latest technologies and focus on quality will thrive. At Hanking Mould, we are committed to maintaining our position as a leader in the plastic moulding industry by continuously investing in research and development, adopting modern practices, and adhering to sustainable methods.
In conclusion, understanding the intricacies of plastic mould manufacture is essential for businesses aiming to leverage this powerful manufacturing technique. With its numerous benefits and ongoing innovations, it is clear that plastic mould manufacture will continue to play a crucial role in various industries for years to come. If you're looking for a reliable partner to help with your plastic injection mould needs, consider Hanking Mould. We bring expertise, quality, and dedication to every project, ensuring your success in this competitive market.